- Cobertura nacional
- comercial@ambraeng.com
- 41 3033 0100
Segurança do trabalho: treinamentos e outras técnicas de implantação
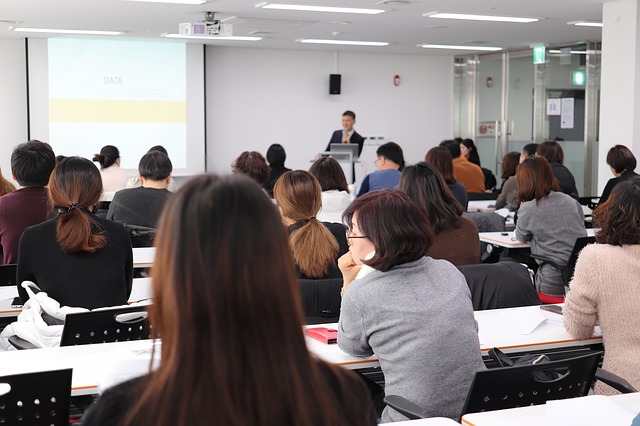
Para ter uma gestão eficaz de segurança do trabalho é preciso ter o colaborador ao seu lado
A segurança do trabalho é um tópico de grande importância para qualquer empresa que tenha uma rotina de — poucos ou diversos — riscos para o trabalhador. Para se ter uma ideia da proporção dos acidentes de trabalho, segundo o Observatório de Segurança e Saúde no Trabalho do Ministério Público do Trabalho (MPT), o Brasil registrou 4,7 milhões de ocorrências no período de 2012 até maio de 2019.
Depois cinco anos em processo de queda, o número de óbitos decorrentes dos acidentes de trabalho voltou a crescer no Brasil em 2018, ano que acumulou 2.022 mortes, em frente às 1.992 de 2017. O país ocupa a quarta posição no ranking internacional de acidentes de trabalho.
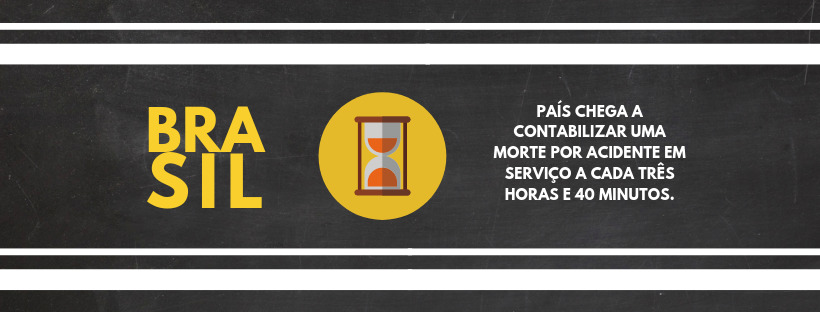
1. Acidentes de trabalho: maior incidência
As atividades que mais incidiram na quantidade de acidentes foram, em primeiro lugar, atendimento hospitalar (378.297 casos); seguido pelo comércio varejista, com predominância de supermercados e hipermercados (142.907); em terceiro, administração pública em geral (119.266); em quarto, a construção de edifícios (104.645); e, por fim, o transporte rodoviário de carga (100.340).
Tenha acesso a mais dados nessa matéria do jornal Extra.
Como consequência dessa condição alarmante, órgãos e empresas se voltam para o aperfeiçoamento de medidas e técnicas de segurança do trabalho. A seguir descubra quais são os benefícios de se investir nessa área e como é possível conscientizar seus colaboradores com eficiência.
2. Benefícios da boa implementação da segurança do trabalho
Em primeiro lugar, uma empresa que oferece condições de segurança para seus colaboradores (confira como fazê-lo no próximo tópico), irá oferecer, por consequência, um aumento na qualidade de vida, já que haverá redução do estresse decorrente do medo ou do risco iminente.
Com isso, é provável que a produtividade também cresça na sua empresa, pois estudos comprovam que trabalhadores felizes são mais produtivos. Apenas observando um ambiente no qual o clima organizacional é mais agradável, no qual os colaboradores são valorizados, é possível notar esse crescimento na produção.
Logo, se o colaborador está feliz e se sente parte importante da empresa, não existe razão para deixá-la. Por isso, há retenção de talentos, o que é fundamental para que um negócio continue a crescer.
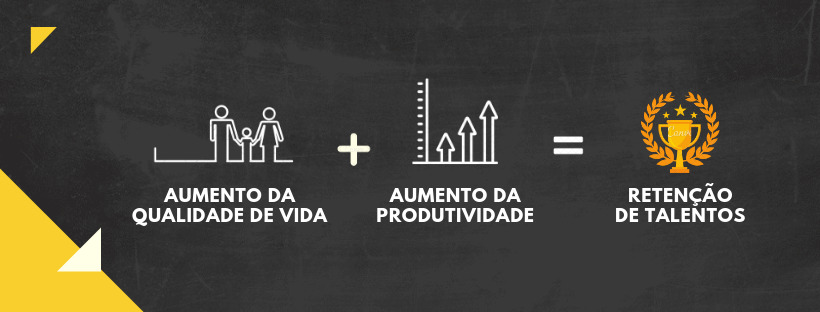
Sendo um lugar seguro e agradável para os colaboradores, a empresa tem sua reputação melhorada, atraindo profissionais ainda melhores e mais comprometido.
Por fim, é claro que uma empresa que investe na segurança do trabalho reduzirá os altos custos decorrentes de acidentes, multas, afastamentos, danos a máquinas e outros.
3. Conscientização do colaborador
Sendo a obrigação da empresa implementar as medidas de segurança do trabalho, é preciso bem orientar o colaborador para que ele entenda a gravidade de possíveis acidentes e como pode melhorar sua atuação, prevenindo ocorrências.
Um dos passos é oferecer treinamentos para esses funcionários. Isso porque, de nada adianta dispor dos Equipamentos de Proteção Individual (EPI) se o colaborador não sabe utilizá-lo corretamente, ou se ele faz pouco caso do uso do mesmo. Portanto, sempre atualize seus colaboradores e faça treinamentos regularmente com novas medidas.
Outro ponto importante é ter uma Comissão Interna de Prevenção de Acidentes (CIPA) realmente atuante. Composta por colaboradores da empresa, a CIPA é obrigatória, porém, muitas empresas ignoram essa regra ou criam a comissão com o mero intuito de cumprir a lei. Uma atuação eficiente da Comissão olha por promover discussões internas, além de repassar informações fundamentais para os trabalhadores sobre a prevenção de acidentes.
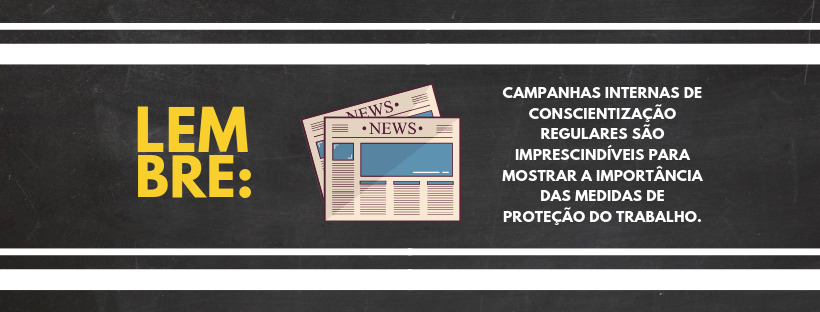
Invista numa equipe de comunicação capaz de criar uma campanha composta por cartazes e avisos, palestras e eventos realmente interessantes, que possuam quórum.
4. Contrapartida da empresa para a segurança do trabalho
A fiscalização é imprescindível, e pode ser um bom termômetro para suas ações. Caso existam muitas falhas dos trabalhadores, é preciso reavaliar se seus treinamentos e campanhas estão atingindo essas pessoas.
Além de tornar o assunto interessante, é necessário que ele seja acessível. Para tanto, é fundamental que a linguagem utilizada na comunicação seja simples, clara e direta. Termos técnicos podem ser substituídos ou explicados a todos.
Adquira equipamentos com empresa de comprovada qualidade técnica no mercado. Não adianta economizar na hora da compra do Equipamento de Proteção Individual (EPI), que tem como objetivo proteger os funcionários de riscos do ambiente de trabalho, evitando ou atenuando possíveis lesões. As sinalizações de segurança também são fundamentais.
>>>Entenda quais são os principais dispositivos de segurança em máquinas e equipamentos — NR12
>>>Saiba mais sobre trabalho em altura e a NR 35
Para que tudo funcione corretamente, a empresa precisa “dar o exemplo” e manter sempre sua fábrica gerida e adequada, pois não basta que o trabalhador tenha consciência, é preciso que ele tenha o suporte necessário. Para se adequar sem sofrimento, você pode contar com a rapidez e o detalhamento da tecnologia.
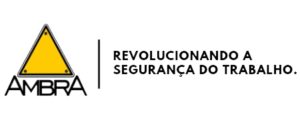
Localização
Contato
(41) 3033 0100
comercial@ambraeng.com